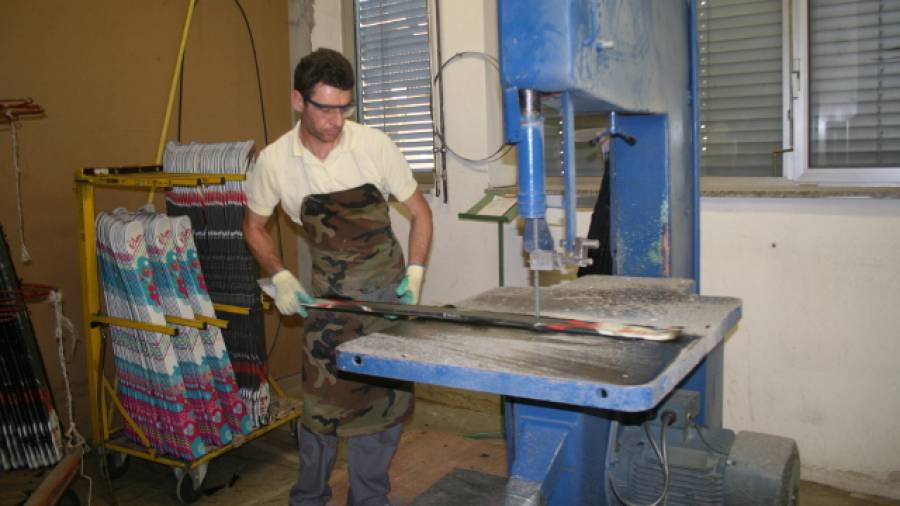
Hinter den Kulissen – So werden Ski gemacht
- Christian Riedel
Rund 2.500 Paar Ski werden beim slowenischen Skihersteller „elan“ pro Tag gefertigt. Es könnten noch deutlich mehr sein und die Zahl war auch höher, aber der Absatzmarkt schrumpft aufgrund der schneearmen Winter und des zunehmenden Skiverleihs. So wurden in Deutschland im vergangenen Jahr rund 280.000 Ski abgesetzt. Vor zehn Jahren waren es noch rund 900.000. Rund dreihundert Mitarbeiter kümmern sich darum, dass die Wintersportler in jedem Jahr mit neuen Brettern versorgt werden. Bis es allerdings soweit ist, muss der Ski erst einmal gebaut werden. Davon schafft jeder Mitarbeiter pro Schicht zwischen 30 und 90 Paar, wobei es eine Rolle spielt, nach welcher Bauart der Ski gefertigt ist.
„Bei elan werden zwei verschiedene Arten von Ski gebaut“, erklärt Bozo Palovsnik, Produktiostechnologe bei elan. „Zum einen gibt es die etwas einfacheren Polyurethan-Ski, die nicht ganz so gute Fahreigenschaften haben. Diese sind einfacher, günstiger und werden oft auch bei Kinderski verwendet. Dank der modernen Schalentechnik haben die Polyurethanski aber deutlich an Qualität gewonnen. Die Schale hat vor allem den Vorteil, dass 3-D-Formen leichter herzustellen sind. Zum anderen gibt es die deutlich aufwändigeren Sandwich-Ski, bei denen verschiedene Schichten aufeinander geklebt werden. Diese sind teurer, haben dafür aber auch deutlich bessere Fahreigenschaften.“
-
Title Title
-
Title Title
-
Title Title
-
Title Title
-
Title Title
-
Title Title
-
Title Title
-
Title Title
-
Title Title
-
Title Title
-
Title Title
-
Title Title
-
Title Title
-
Title Title
-
Title Title
-
Title Title
-
Title Title
-
Title Title
-
Title Title
https://netz-athleten.de/lifestyle/sports-inside/item/4516-hinter-den-kulissen-so-werden-ski-gemacht#sigProId7539e8b9ac
Polyurethan-Ski
Für beide Ski-Arten benötigt man zunächst eine Alu-Form. In diese wird bei den Polyurethan-Ski zunächst die Lauffläche und die Kanten gelegt. Die Kanten wurden vorher bereits entsprechend gebogen und zugeschnitten. Je nach Art des Skis wird ein Holz- oder ein Laminat-Kern darauf gelegt. Dann wird eine Oberfläche oder die Schale darauf gegeben und mit flüssigem Polyurethan, also Kunstharz, aufgefüllt. „Vor dem Füllen wird der Ski luftdicht verschlossen. Wichtig ist, dass der Ski vorher mit Druckluft mit einem Druck von 6bar gefüllt wird“, sagt der Skibauer. „Dann wird die Schale zusammengepresst und erst dann wird der ebenfalls unter Druck stehende Schaum in die Form gespritzt. Da der PU-Schaum wie ein Pilz aufgeht, sobald er aus dem Schlauch gespritzt wird, würde er den Ski sprengen, wenn er nicht schon unter Druck stehen würde. Deswegen braucht der Schaum eine Sperre, in der er hart werden kann.“
Sandwich-Ski
Grundlage für den Sandwich-Ski ist ein Holzkern, der schon vorher angefertigt, gefräst und geschliffen wird. Auch dann benötigt man wieder eine Aluform, in der die einzelnen Schichten aufeinandergelegt werden. Bei einem guten Ski können es mit Lauffläche, Holzkern, mehrere Schichten Nass-Laminat, Aluminiumlamellen und der Oberfläche Bis zu acht Schichten sein. Im vorderen und hinteren Bereich kommen noch einmal separate Teile für die Spitze bzw. die Ferse hinzu, die dem Ski die besonderen Fahreigenschaften verleihen sollen. „Sind die Teile aufeinandergeschichtet, kommt der Ski in die Presse“, erklärt Bozo. „Hier wird er rund 15min bei 110 Grad gepresst, bevor er in seiner Grundform fertig ist.“
Nach dem Pressen
Viele Arbeitsschritte werden bei elan von Hand durchgeführt. So werden sämtliche Schichten von Hand aufeinandergelegt, die Maschinen werden von Hand bedient und auch nachdem die Ski aus der Presse kommen, wird viel von Hand gefräst und geschliffen. Auch die Kontrolle erfolgt mit Augenmaß und Fingerspitzengefühl. Nur ein Teil der Produktion ist automatisiert. Wenn man so will ist ein großer Teil der Skiproduktion noch echte Handarbeit.